When most people think about safety tech, they think about the moment it matters: a gas leak detected, an SOS alert triggered, a worker protected.
At Blackline Safety, our Quality Assurance team focuses on everything that leads up to that moment. Because protection doesn’t start in the field—it starts on the bench, in the lab, and on the line.
And it all starts with quality.
Quality That Scales
Our quality system is built to scale with us—and with our customers. In the last four years alone, we’ve:
- Increased test time per device by 650%
- Expanded our QA team by over 250%
- Invested $2 million into Surface Mount Technology (SMT) and inspection tools to bring more testing in house, giving us more oversight and control from earlier in the manufacturing process.
Because our Quality team is located just steps from our manufacturing floor, we have tighter oversight into what’s happening in real-time—and can react more quickly when issues are found. This level of integration is hard to achieve when production is outsourced or located overseas.
Design It Right, Test It Hard
Before a device ever ships, our Quality team puts it through its paces—early, often, and aggressively.
We verify that the product matches design intent. We validate it against real-world customer needs. And we test its reliability like it’s already in the field.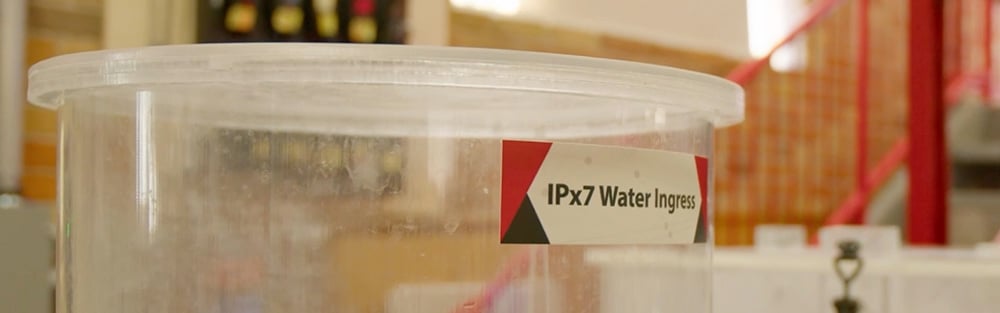
Our devices face conditions that simulate the most punishing environments our customers operate in, including:
- Ingress testing to confirm IP compliance:
- IPx7, which assesses the device's ability to withstand water immersion. Specifically, an IPx7 rating means the device can be submerged in up to 1 meter of water for 30 minutes without suffering harmful effects.
- IP6x, which assesses the device shell’s ability to prevent dust from entering and potentially damaging the internal components. An IP6x rating signifies that the product is dust-tight, meaning no dust can penetrate the shell. This is achieved through rigorous testing in a dust chamber where the product is exposed to a controlled flow of fine dust particles.
- Thermal extremes from -40°C to +60°C
- Thousands of automated Dock insertions and button presses
If it breaks, we want it to break here—not out there.
But performance isn’t just about surviving a few extreme tests. It’s about building reliability into the product from day one—so it lasts longer, even in the harshest conditions, and earns its keep in the field.
Our 68-Point Testing Protocol
Every Blackline device runs a 68-point quality test before it ships. No exceptions. This process spans 10 categories, including:
- 2D and 3D SMT inspections using automated optical inspection
- Functional testing for radios, sensors, alarms, and behavior under load
- Burn-in and extended use testing to catch early-life failures
- Connectivity checks across cellular and satellite networks
- Calibration and bump test validation
- Final configuration and assembly verification
The tests are a mix of automation and hands-on inspection that gives us both speed and certainty that the devices leaving our floor are ready for the field.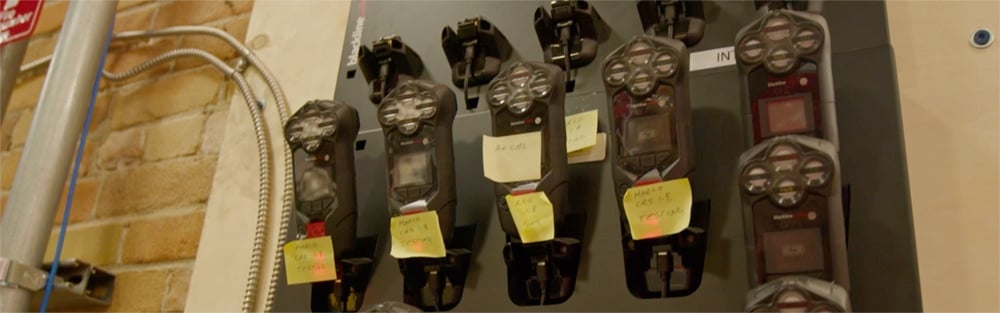
What Happens When a Device Comes Back
Sometimes devices come back—end-of-life, rental returns, warranty claims, unexpected field behavior. When they do, our Customer Quality team steps in.
First, we investigate the reported issue. Then, the device is put through a fresh round of diagnostics:
- Physical and internal inspections
- Hardware tests (vibration motor, speaker, microphone, etc.)
- Connectivity checks
- Functional testing, including calibration and emergency alerts
If it meets our criteria and passes all of the above, as well as another round of the full 68-point test, it’s refurbished and returned to advanced replacement stock. If it fails even a single one of the above criteria, it’s responsibly recycled.
But we don’t stop there. Every returned device adds to a growing pool of data. We track patterns, flag trends, and feed those insights directly into Product Development, Product Management and Manufacturing improvements so the next generation of devices is that much better.
Engineered for Accountability
Every test and check in our QA process comes down to one simple question: will this device keep someone safe when it counts?
At Blackline, quality assurance isn’t about ticking boxes – it’s about protecting the lone worker in a remote oilfield, the firefighter charging into danger, the technician maintaining a power grid in a storm.
Our team knows that behind every detector or monitor is a person trusting it with their life. That’s why we refuse to compromise on quality and build every device like someone’s life depends on it—because it does.